Keeping
Good Records is fundamental to efficient
operation of a telephone
company, both for efficient management of resources and for smooth
dealings
with customers, regulators and others, - - - suppliers, for
instance.
Where record keeping suffers, it often is because the company outgrew
the
system, which may have been designed when the company was tiny and
clearly
didn't need a lot of "unnecessary paperwork".
....Office
routines differ greatly in different sized companies. but they all
share
the same common goals: to supply all customers with high quality
service
at the lowest cost; and to provide the company investors with the
highest
return possible on their investment, consistent with the first goal.
....Each
of these two goals includes several components. Thus, the goal of
providing
high quality services means: 1) establishing the service promised; 2)
keeping
circuits clear, strong and trouble free; 3) restoring interrupted
service
as quickly as possible; and 4) providing accurate billing (not within
the
scope of this text.)
....Similarly,
giving company investors the highest possible return depends on: 1)
being
able to connect or restore service quickly, without error; 2) making it
possible to use fully each unit of plant in place; 3) using orderly
company
procedures to help employees do their best; 4) supplying engineering
personnel
with accurate information on maintenance problems, plant traffic, fill
and actual costs; and 5) keeping on hand only the required stock.
....The
trend that ties these components together is record keeping. Because
records
are vital to the efficient operation of the company - - - whether
it is plant, engineering or customer records, it is important that all
personnel, craft and administrative, have a good understanding of the
needed
forms and records in order to help them do their jobs better and keep
the
basic system up to date. Not only will such an understanding give telco
personnel ideas on how to improve their own routines, it will help them
contribute to achieving the basic company goals.
Purchasing
....Purchasing
is the process of ordering, paying for and stocking an item of
material.
It is the first action taken after a careful decision has been made to
add a section or item of telephone plant, or to add to the stock of
in-site
supplies.
....Telephone
plant can be purchased in two ways, through a contractor or by
purchasing
material through a supplier and placing it with your own crews. When
plant
is purchased by contract, the contractor's invoice includes an itemized
list of each unit's cost. the units are debited to a Construction in
Progress
account where you may have to add some of your own costs or your
engineer's
costs to the unit's cost. In ordering your own plant, the quantity,
type,
size, and cost for large plant additions should be made to you by the
engineer.
....Controlling
the costs of purchases is a must these days. Consider three ways to do
this: 1) Call each supplier and obtain the current prices. 2) Have the
supplier keep you posted on current prices. 3) Use your experience on
which
supplier has the lowest price on each item.
....The
inventory record form also should be arranged so the quantity in stock
and the timing of order placement can be controlled, thereby making it
possible to budget costs through the year.
....In
the past, the person responsible for making purchases may have handed a
list to a supplier making a routine call. Or the purchaser may have
telephoned
the supplier to give the order. These actions should be practiced only
in emergencies. Instead, have printed your own company pre numbered
ordering
form. Use it for all purchases made. See
Figure
1 Doing this, you will always know what you actually ordered,
when
you ordered and why you ordered. Finding what you ordered, when there
is
a question, will be simplified because you follow a set routine
in
making purchases.
....If
you are an REA borrower, have your assigned number set in the heading
of
your order form, with instructions on the back. This way, you will have
on each order, written notice to the supplier that the items shipped
must
be approved items.
....Remember
to have your inventory record in front of you when making out an order.
Always check it to make sure that you have not missed an item.
....All
orders must be approved by the manager or by an assigned agent. Copies
should be distributed within the company to three points. One
is
the person responsible for receiving the material. This person will
know
exactly what is being ordered, have an idea when it will arrive and to
whom it is to be delivered. A second copy should go to
"accounts
payable", so they will know who has ordered material, what item is
expected
and what cash should be available to pay for the purchase. A third
copy should go to persons responsible for completing a project, so it
is
known that the project is being followed through, as
planned.
....If
material must be ordered by telephone, have a purchase order number
ready,
telephone the order and give the supplier the order number. Then send a
copy of the order to the supplier, confirming the call, and handle the
order within your company as a normal order. This will keep the routine
normal, both at your company as well as at the supplier's offices.
....Some
companies, especially those with district offices, must have a form
which
precedes the making of a purchase order. This is called a Material
Requisition. See
Figure 2 Small companies may type a purchase order from a list
written on a scratch pad; however, the larger company's purchasing
department
must know permission has been given before the typing of a purchase
order
is done. The requisition form therefore is necessary. Telephone
orders
must be confirmed in requisitions also. You may even have to call long
distance to your purchasing department to obtain an order number. Keep
the routine normal.
When
the Order Arrives
....Receiving
material is the process of opening freight or parcels, checking the
enclosed
packing slip against the actual contents and filling out the Record of
Receiving form See Figure 3. This
form
sets up a consistent routine on keeping a good record of material.
Also,
this form makes it possible to eliminate indicating which account or
accounts
a check is made out for, only the receiving number need be recorded on
the supplier's paycheck. Of course, only one supplier's material can be
recorded on any one Record of Receiving.
....Having
the person who receives the material, fill in the stock numbers is more
reasonable because that person usually is more knowledgeable about the
material. The spaces marked "A" on the sample in Figure 3 will
be
filled in by the receiver. The packing slip then is kept in the
receiving
files, or it can be sent as a notice of receiving to persons
responsible
for a specific project.
....Accounting
personnel, filling in the spaces marked "B", will use the form
further
to price out the units, pay for them and then transfer the costs to the
proper accounts.
....Paying
for units of a contract also can be achieved on the Record of Receiving
from. The contract units then are transferred to a Construction in
Progress
account.
....When
receiving and checking a shipment reveals an item that cannot be used
because
it is damaged or it is the wrong item, place a "D" for damaged or a "W"
for wrong in the Condition column. Then set the item aside and make
arrangements
to have it returned. The Notice of Goods Returned or Transferred form
then
is filled out See Figure 4. The
company
still will receive an invoice for all the items shipped and pay it in
full.
A credit will be issued by the supplier for goods returned. The
Accounting
department keeps the goods returned form on file, which is a record of
cash paid out, even though it is not put into inventory. Checking this
file periodically can reveal any credit not honored, and then proper
steps
can be taken to see that credit is issued. This form also is filled in
by the person sending the goods spaces marked "A" and accounting
marked "B".
Inventory
....Inventory,
to company supervisors and executives, means to have materials or a
record
of materials in stock, ready for labor employees to place in plant.
Inventory,
to a labor employee, can mean that he or she will count and list all of
the material in stock on a given day each year. Both of these
definitions
are correct; however, a more meaningful one is that inventory is money
invested, which the company cannot earn a return on.
....It
takes a pretty good plan to keep the inventory down and have material
in
stock when it is needed. You have to know when you can buy at a larger
quantity in order to cut purchase cost. There must not be excess
material
that will sit around for years. Also, if money is not spent, it is
available
for other needs or is in the bank earning interest. Nowadays, there are
suppliers who give good prices on small quantities and can give 24 hour
delivery. Shop around.
....There
can be three methods used to keep a record of your stock. One
is
to keep count and cost of each separate item you buy until it is
actually
working in plant. The second is keep count and cost only of the
items which are identifiable as installable units, then combine the
costs
of the small items, such as screws, tape, etc., into an Exempt Material
account. The exempt material costs are spread by percent of average
use,
over several accounts. The costs do not need to be on record as being
in
stock. The third method is not to put the material cost on
inventory
but charge it directly to a Work Order in Progress account and store
the
item in a separate location until it is in plant. This is not a good
practice
because some person may pick up an item and put it in plant somewhere
else
by mistake, or even if he knows he should not do it. Use this third
method
only with vehicles tools, etc.
....The
first inventory method should be used at warehouses where the small
items
move quickly as large items, and the inventory must be on hand to
distribute
to branch or district stockrooms. However, it may be necessary to
inventory
all items if there has been a history of theft or overstocking, using
this
method only until the problem has been corrected. The large stockroom
may
do all items also, but costs in bookkeeping still will not include
exempt
items. There are extra costs encountered by counting and reporting the
use of each screw and bolt: (1) it requires one third more time to fill
out a time report or cost out a work order; (2) it takes twice the time
to keep inventory throughout the year; (3) in a small company, all
stock
would have to be locked up, making it necessary to have one person
available
full time to distribute material.
....The
use of the exempt material method is recommended for all companies with
more than 2000 stations. The cost difference for smaller companies to
record
all items will not be significant, and they still may elect to use that
method, if law permits.
....Inventory
procedures must be set up so that transfer of costs and materials from
stock are easily understood and free from errors. The process starts
with
the receiving of material. After the material is received and placed on
the inventory record, it is ready to be distributed.
....As
previously mentioned, the cost record of the material will end up in a
ledger book, by account. To aid the process of transferring the costs,
it is best to assign stock numbers to each item on inventory. The
numbers
can be made up of five, six or seven digits, whichever works best. They
should be designed to be descriptive of the piece of material. The
engineer
then can use the number on the work order plans, which in turn tells
the
laborer what unit to place. The laborer then can place that same number
on his or her time sheet, without having to check which number to use.
....The
first two "digits" in the stock number should be letters that describe
the type of unit it is. The remaining digits describe size, in the
metric
system, where applicable, If the first two letters can be the same as
property
records, use them.
Examples:
CA10124
.......4
= 24 gauge
012 = 12
pair
........1
= AP sheath
CA =
cable..
|
ST10039
.......039
= 30 millimeter
.....10
= galvanized
.ST
= strand...
..
|
SC20025
025 = fits cable
up to..
...............25
millimeters in dia.
20 = for
plastic
fig. 8
SC =
splice closure..
|
|
....The
stock numbers must be placed on labels which are on the shelf under
each
item in the store room. The daily time sheet must be designed to accept
these numbers and so should service orders and work order closings.
....The
example shown in Figure 5 is for a splice closure. When the inventory
is
down to about four, order 12 more. The card should be made of a
material
which can be written on or changed.
.......................................................................
|
The label also should
be used for exempt material. In place of the stock number, place
a description of the material.
Example: Screws, Stainless steel,
round 3/4 x 8.
A careful study and
plan, made by the manager, plant superintendent and accounting is
needed to fill in the maximum and minimum quantities. Each year's
inventory will show if the plan is working well.
If your stock shelf's are too thin for this
label, the manufacturer's name and number can be moved up to the right,
or it could be removed. The reason for listing the manufacturer is to
eliminate having to look in the catalog.
Exempt
Material:
Material being invoiced which is
commonly used on many different items or parts of items but is costly
to inventory is partially charged to an Exempt Material Account and the
remainder is spread over Maintenance. As inventoried items are put to
use in plant through a work order or service order, Exempt Material is
also charged out. The ratio of total inventory in stock in relation to
total exempt material in stock, is applied to the inventory just placed
in plant. The result is the value to be credited from Exempt Material
and charged to Plant.
The ratio used
will not remain the same because of the continual purchases being made.
If more exempt material is purchased, more will be charged out.
The card used to keep record of each different
inventory item can be used to keep the balance of
|
|
exempt material. This card will be
described later in the series.
The invoice which contains one or more units
of exempt material could have the quantity spread figured out on the
back of the invoice. The payment check then could be charged to each of
the spread accounts. However, this takes many more entries to the
ledgers and also can take up too much space on the check stub.
When filling out the
receiving report (Figure 3),
note that at the right edge there is a column to place a Material
Holding account number. This account is used to combine several
invoices before spreading the costs to Exempt Material or Maintenance.
At the left of the account numbers is a column to place a code which is
used to tell how a cost is to spread from the Material Holding account.
Figure 6
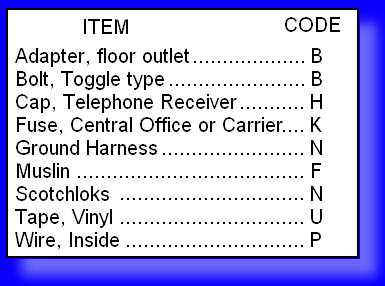 |
|
Figure
6 lists some units with code letters. A sheet used to spread the
material in holding, according to the code, is shown in Figure 7. The
total cost, listed just left of the code number on the receiving
report, is placed on the spread sheet under the corresponding code.
Receiving report costs, with several units of the same code, are added
together, with that total being placed on that spread sheet.
A routine time is picked to credit this holding account
and debit
the Maintenance or Exempt Material accounts. On your spread sheet,
total each coded column and spread that total according to the
percentages noted within the boxes below, placing the broken down costs
in
|
the boxes. Each horizontal line then is
totaled to the left, giving
you the total cost to debit the noted account.
The
percentages used to spread each column are the results of a careful
study made by your personnel as to where each piece of material might
be used in maintenance. For example, vinyl tape is placed in column
"U", 20% is used Exempt Material, 20% is used for the repair of aerial
cable, 20% for buried cable, 10% for central office or carrier and 30%
for station connections. Is this right? You had better find and back
your own figures, or use the REA recommendations.
Go To Book
Index
|